THE CHALLENGE
A wood pelletizing plant encountered operational challenges with sawdust storage. As sawdust and other wood materials were added to the silos, the weight caused build-up and blockages that can lead to overheating of kiln dryers used in the production process. To help prevent the risk of fire, plant operators used manual intervention to periodically remove the build-up. This disrupted production and created operational inefficiencies.
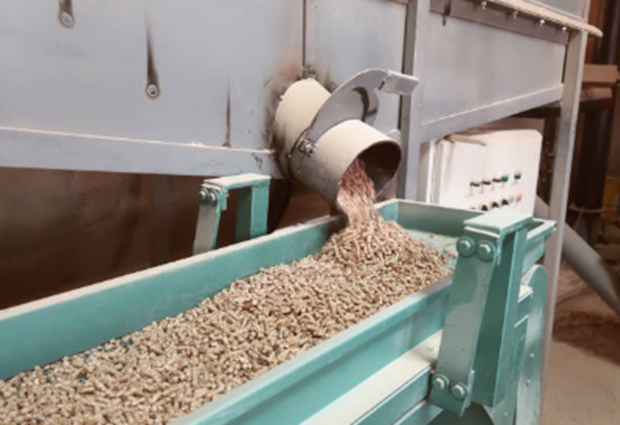
THE NEED
The plant needed a solution to both monitor and control the flow of wood material to prevent blockages, and detect if chutes were plugged.
There was also a unique additional need the client had – to be able detect metal from entering the pelletizing machine. The metal, from the paddlewheel, had a risk of detaching from its unit. If this separation occurred it would not only destroy the pelletizer equipment, but pieces of metal would end-up in the final product – resulting in production needing to restart and creating a lack of quality control.
THE WAJAX SOLUTION
To help address these safety and operational challenges, Wajax partnered with the client to assess the best customized solution. This included the provision of numerous multi-vane paddle Roto-Bindicator™ Pro detectors.
With adjustable sensitivity, these detectors can determine high and low levels within silo sawdust storage, as well as sawdust conveying and pellet storage silos.
Wajax also ensured a magnetic paddlewheel was incorporated, which can be captured by a magnetic separator in the event of a paddle separation from the electronics housing to prevent pelletizer destruction.
THE IMPACT
Operators now had instant visual feedback to control sawdust levels to help prevent blockages, as well as functional diagnostics that could detect a unit fault such as metal being buried in material.
With Wajax’s technical and safety expertise, the new system was not only able to reduce the risk of fire and help increase safety for personnel, but also enhance operational productivity for the client.
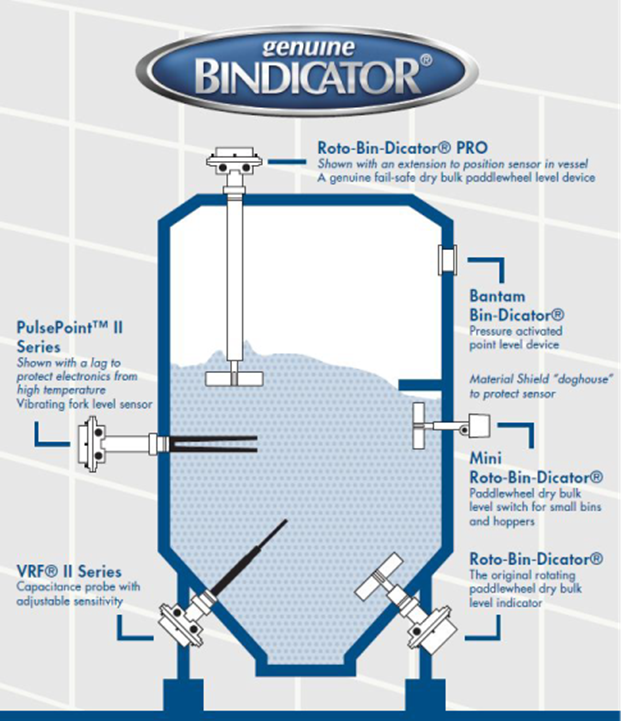