THE CHALLENGE
An Eastern Canadian mining customer was gearing up to reopen production at a mine that had been inactive for years. This significant undertaking would require everything from mining equipment and machines to repair audits, logistics, inventory, and countless other necessities.
Opening and operating a mine is a complex process. Everyone needs to be on the same page to ensure deadlines are met. This project had significant barriers to start-up, with all the mine’s previous operating data, such as inventory, maintenance schedules, etc., being obsolete and unusable. The lack of information put our customer at a considerable disadvantage and threatened to derail the entire operation.
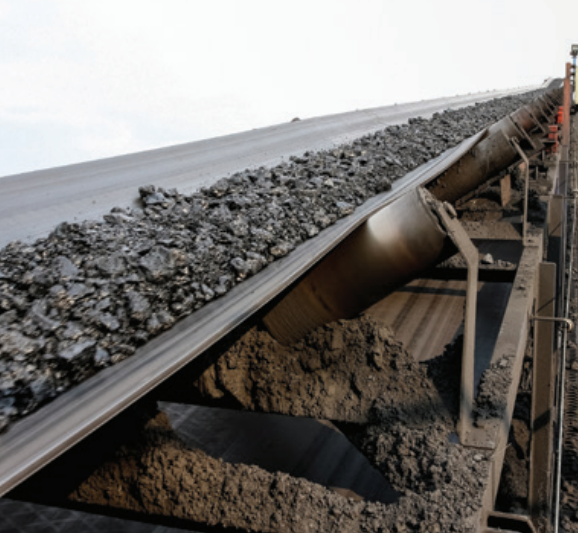
THE NEED
Wajax was required to support all aspects of the mining operation, from the ground up; finding the necessary mining equipment, conducting audits, setting up supply chains, taking inventory, collecting data, and establishing a trustworthy ERS inspection and repair program. All of this needed to be done efficiently, within the tight timeframe. An oversight could result in delays that would cost the mine hundreds of thousands of dollars.
OUR SOLUTION
The vast project scope created an ideal opportunity to demonstrate the efficiency, productivity, and capability of the One Wajax solution. Meeting the customer’s aggressive deadline required the rapid mobilization of many resources. Wajax engineers and specialists conducted equipment audits, heavy equipment inspection and inventory control. Since there was no reference data, our team had to start from scratch, going into the field to conduct their audits and inspections.
We created a highly functional inventory system, establishing the quantities, critical on site inventory, and other vital aspects. Our ERS team conducted repairs in all essential areas of operation. Many pieces of equipment such as the conveyor systems, critical gearboxes, idlers, crushers, and pumping systems were no longer in production, making it impossible to purchase replacements. Creative solutions were required. Each piece of equipment was reverse engineered in order to repair it and ensure it would be fully operational on day one. We then provided construction equipment, including Hitachi loaders and excavators, and Hyster® cranes and aerial lifts.
As this was underway, additional work was conducted; equipment audits were completed on bearings, power transmissions, hoses and fittings, hydraulics, pneumatics, and personal protective equipment. As the finish line approached, we got to work training maintenance crews, storeroom employees and preparing 400 employees with the proper personal protective equipment.
THE IMPACT
There were many obstacles our customer had to overcome to get their mine back into production, and with help from the One Wajax solution, they were able to do it. From the first walk-through to the final hire, we worked in tandem, keeping all parties well informed every step of the way.
Having made improvements with future growth in mind and with a solid operational structure, our customer is now well aligned for future expansion. Our team of engineers and specialists worked incredibly hard, put in some long hours, and showed some remarkable ingenuity to get the mining operation up and running.
For more innovative mining solutions please visit our industry page.