Our world-class products, combined with our broad industry experience and engineering capabilities, allow us to support our customers in meeting their environmental objectives. We provide around-the-clock assistance to ensure that customers not only keep their operations running at peak performance but also reduce energy consumption, emissions and waste.
Through the incorporation of IOT and other remote monitoring solutions, we are able to support efficient lifecycle management and predictive / proactive maintenance. This helps our customers reduce both greenhouse gas emissions and waste, allowing them to remain compliant with increasingly strict global standards.
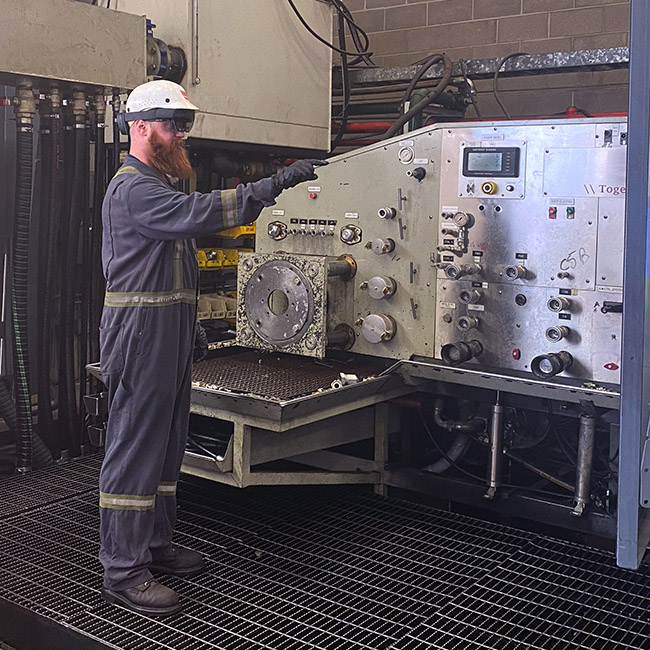
Waste Reduction
Reducing waste during the manufacturing process is a critical action item for many of our customers on their journey to minimizing their overall environmental impact. Additional benefits of reducing waste can include reducing costs and your carbon footprint by limiting various emissions.
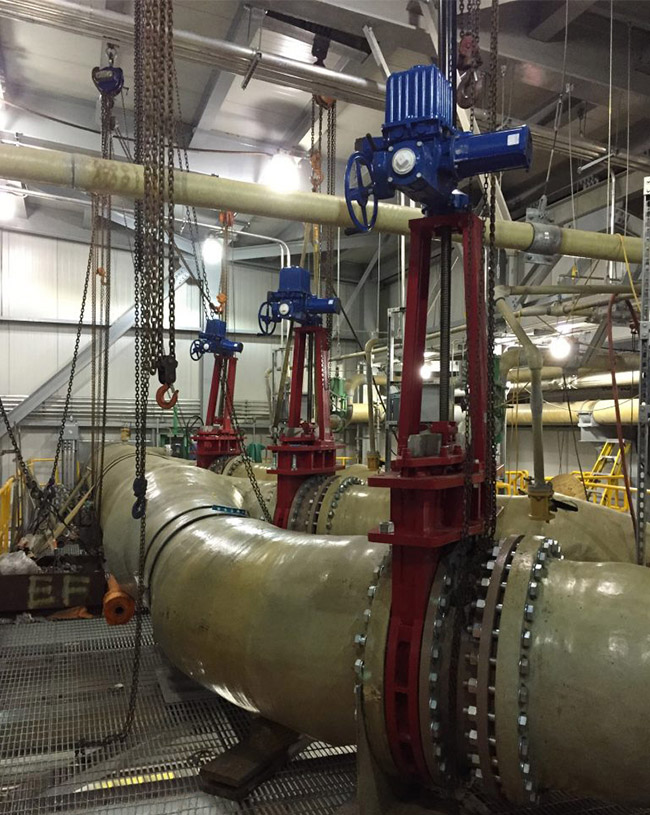
St Mary’s Cement
An example of when the Wajax team used our waste reduction expertise can be seen in the work we did for one of North America’s oldest cement companies – St Mary’s.
By providing this customer with robust gate valves, we helped them recycle a large portion of the kiln dust their manufacturing process produced. Using waste heat, the by-product of this process could be turned into a sellable fertilizer for a complete solution. These valves also helped reduce the emissions of several hazardous compounds, like sulfur dioxide and hydrogen chloride from the cement kiln.
Take a look at the project case study for more details.
Batter Escape From Bakery
There are also occasions when our customers need help in optimizing manufacturing systems to reduce material waste. This was seen in our client’s large-scale, 120,000sqft bakery production facility in Ontario. Their problem was batter seepage through their existing rotary lobe production pumps – something that also presented a slip hazard for employees.
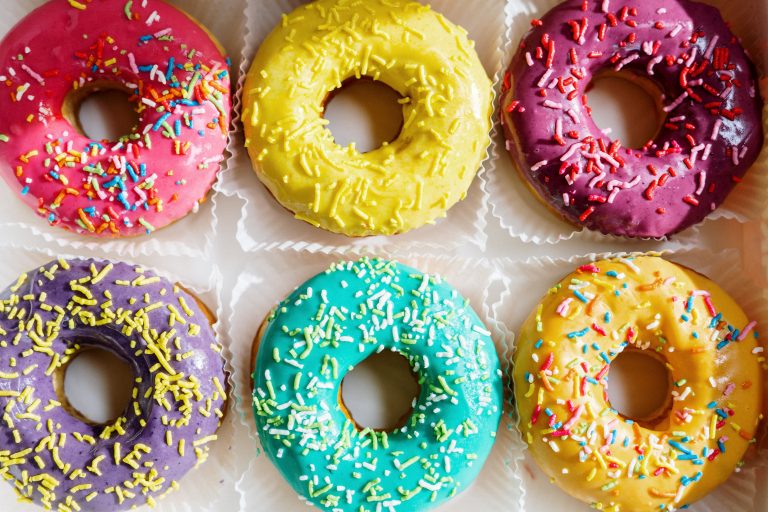
The ‘leak-free’ Wajax solution eliminated the need for time-consuming maintenance and significantly reduced production loss. An ideal outcome for a company that simply could not keep up with the cost of lost materials.
Check out the case study for more detailed information on this project.
The Wajax team has the know-how and experience needed to identify and implement systems that eliminate waste and help our customers meet their sustainability goals. If you need help in this area, please don’t hesitate to contact us.