THE CHALLENGE
One of Wajax’s customers is a leading eastern Canadian paper manufacturer, operating facilities all over the country. For over 50 years, they have supplied some of the top publishing organizations in North America. One Friday evening, their plant in Newfoundland encountered a serious issue. The Babbitt bearing for a vacuum pump on paper machine #7 failed, and they didn’t have a spare bearing. Without this vacuum pump running, production on paper machine #7 was severely impacted.
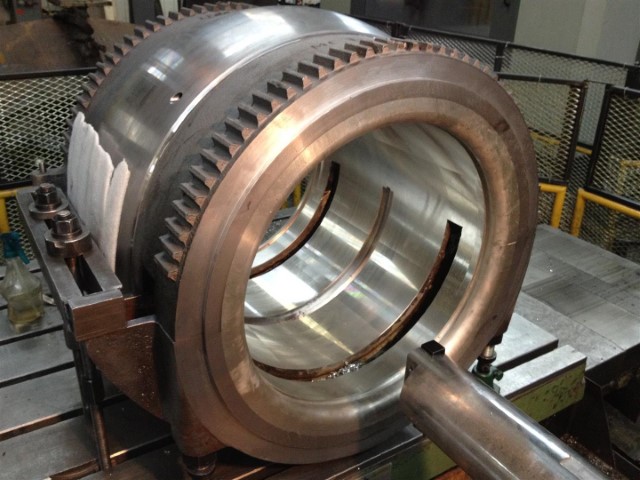
THE NEED
The paper manufacturer required the Babbitt bearing repaired, but what they needed even more was time: every day without the bearing cost operations up to $6000. The bearing needed to be shipped from Newfoundland to Montreal, be repaired, and then shipped back as soon as possible — a job that typically takes over a month.
THE WAJAX SOLUTION
As soon as our customer told us the issue, we got in contact with our Delom team to go over a plan of action. The bearing arrived in Montreal on a Sunday, and we arranged to have someone waiting at the airport ready for its arrival. Once received, we had crews working 24/7 to get the job done. Status reports were exchanged regularly between Wajax and Delom to ensure everything was running smoothly.
THE IMPACT
This was a real test of Wajax’s manufacturing capabilities. Companies that offer Babbitt bearing manufacturing and repair are difficult to find, and the process is known for having very long delivery times. Under normal circumstances, a job of this magnitude would take five to six weeks to complete. Wajax and Delom completed it in two, saving the customer over $100,000.
Not only did our customer get their Babbitt bearing repaired and returned in a fraction of the time, but they saw firsthand how efficiently Wajax operates. Our Delom team fabricated additional seals for the bearing in house, saving countless hours. Working smart and hard, Wajax proved itself to be a partner you can trust and rely on when it matters most.
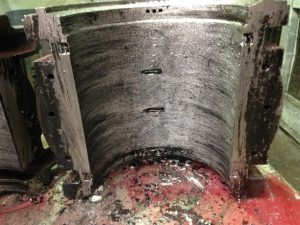
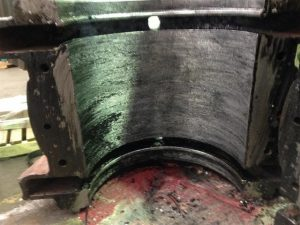